United States
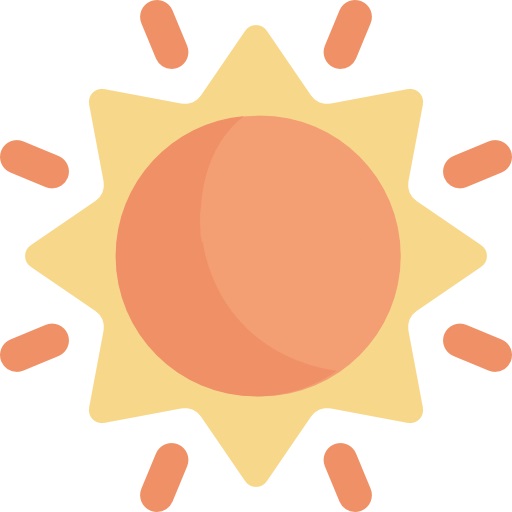
Bright Outlook
Yes
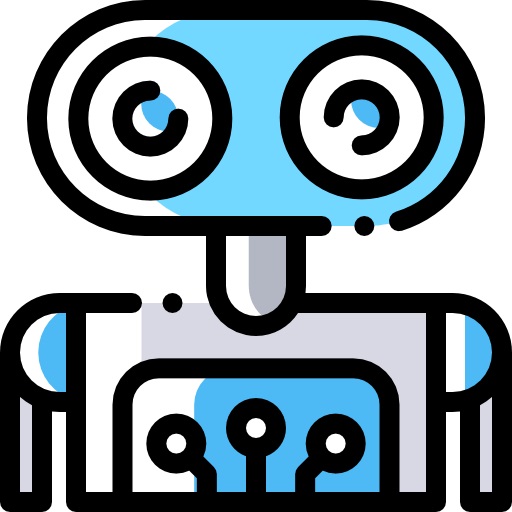
Automation Impact
High
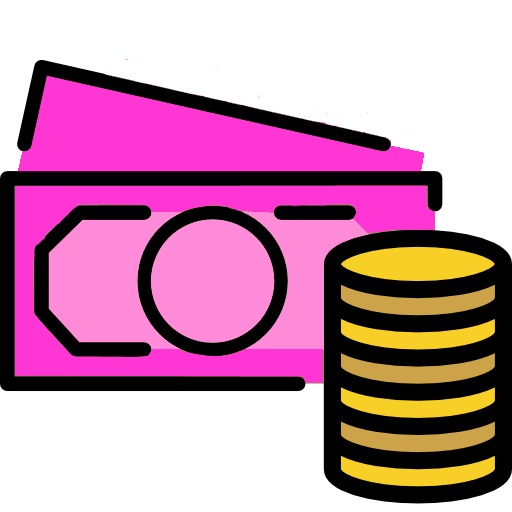
Salary Level
AverageTitle | Job Zone Three: Medium Preparation Needed |
---|---|
Experience | Previous work-related skill, knowledge, or experience is required for these occupations. For example, an electrician must have completed three or four years of apprenticeship or several years of vocational training, and often must have passed a licensing exam, in order to perform the job. |
Education | Most occupations in this zone require training in vocational schools, related on-the-job experience, or an associate's degree. |
Job Training | Employees in these occupations usually need one or two years of training involving both on-the-job experience and informal training with experienced workers. A recognized apprenticeship program may be associated with these occupations. |
Examples | These occupations usually involve using communication and organizational skills to coordinate, supervise, manage, or train others to accomplish goals. Examples include food service managers, electricians, agricultural technicians, legal secretaries, interviewers, and insurance sales agents. |
SVP Range | (6.0 to 7.0) |
- Majority (39.46) percent of respondents had : High School Diploma (or GED or High School Equivalence Certificate)
- Some (25.44) percent of respondents had :Some College Courses
- Some (21.26) percent of respondents had :Post-Secondary Certificate - awarded for training completed after high school (for example, in Personnel Services, Engineering-related Technologies, Vocational Home Economics, Construction Trades, Mechanics and Repairers, Precision Production Trades)
Interest Code : RCI
- Realistic-Realistic occupations frequently involve work activities that include practical, hands-on problems and solutions. They often deal with plants, animals, and real-world materials like wood, tools, and machinery. Many of the occupations require working outside, and do not involve a lot of paperwork or working closely with others.
- Conventional-Conventional occupations frequently involve following set procedures and routines. These occupations can include working with data and details more than with ideas. Usually there is a clear line of authority to follow.
- Investigative-Investigative occupations frequently involve working with ideas, and require an extensive amount of thinking. These occupations can involve searching for facts and figuring out problems mentally.
- Arm-Hand Steadiness-The ability to keep your hand and arm steady while moving your arm or while holding your arm and hand in one position.
- Problem Sensitivity-The ability to tell when something is wrong or is likely to go wrong. It does not involve solving the problem, only recognizing there is a problem.
- Near Vision-The ability to see details at close range (within a few feet of the observer).
- Oral Comprehension-The ability to listen to and understand information and ideas presented through spoken words and sentences.
- Written Comprehension-The ability to read and understand information and ideas presented in writing.
- Information Ordering-The ability to arrange things or actions in a certain order or pattern according to a specific rule or set of rules (e.g., patterns of numbers, letters, words, pictures, mathematical operations).
- Attention to Detail-Job requires being careful about detail and thorough in completing work tasks.
- Dependability-Job requires being reliable, responsible, and dependable, and fulfilling obligations.
- Initiative-Job requires a willingness to take on responsibilities and challenges.
- Cooperation-Job requires being pleasant with others on the job and displaying a good-natured, cooperative attitude.
- Independence-Job requires developing one's own ways of doing things, guiding oneself with little or no supervision, and depending on oneself to get things done.
- Innovation-Job requires creativity and alternative thinking to develop new ideas for and answers to work-related problems.
Top 3 Values
- Support-Occupations that satisfy this work value offer supportive management that stands behind employees. Corresponding needs are Company Policies, Supervision: Human Relations and Supervision: Technical.
- Independence-Occupations that satisfy this work value allow employees to work on their own and make decisions. Corresponding needs are Creativity, Responsibility and Autonomy.
- Relationships-Occupations that satisfy this work value allow employees to provide service to others and work with co-workers in a friendly non-competitive environment. Corresponding needs are Co-workers, Moral Values and Social Service.
- Operation Monitoring-Watching gauges, dials, or other indicators to make sure a machine is working properly.
- Equipment Maintenance-Performing routine maintenance on equipment and determining when and what kind of maintenance is needed.
- Repairing-Repairing machines or systems using the needed tools.
- Troubleshooting-Determining causes of operating errors and deciding what to do about it.
- Operation and Control-Controlling operations of equipment or systems.
- Reading Comprehension-Understanding written sentences and paragraphs in work related documents.
- Mechanical-Knowledge of machines and tools, including their designs, uses, repair, and maintenance.
- Mathematics-Knowledge of arithmetic, algebra, geometry, calculus, statistics, and their applications.
- Design-Knowledge of design techniques, tools, and principles involved in production of precision technical plans, blueprints, drawings, and models.
- English Language-Knowledge of the structure and content of the English language including the meaning and spelling of words, rules of composition, and grammar.
- Engineering and Technology-Knowledge of the practical application of engineering science and technology. This includes applying principles, techniques, procedures, and equipment to the design and production of various goods and services.
- Administration and Management-Knowledge of business and management principles involved in strategic planning, resource allocation, human resources modeling, leadership technique, production methods, and coordination of people and resources.
- Start machines and observe mechanical operation to determine efficiency and to detect problems.
- Read work orders and specifications to determine machines and equipment requiring repair or maintenance.
- Inspect or test damaged machine parts, and mark defective areas or advise supervisors of repair needs.
- Reassemble machines after the completion of repair or maintenance work.
- Dismantle machines and remove parts for repair, using hand tools, chain falls, jacks, cranes, or hoists.
- Install, replace, or change machine parts and attachments, according to production specifications.
- Collaborate with other workers to repair or move machines, machine parts, or equipment.
- Inventory and requisition machine parts, equipment, and other supplies so that stock can be maintained and replenished.
- Record production, repair, and machine maintenance information.
- Set up and operate machines, and adjust controls to regulate operations.
- Repairing and Maintaining Mechanical Equipment-Servicing, repairing, adjusting, and testing machines, devices, moving parts, and equipment that operate primarily on the basis of mechanical (not electronic) principles.
- Inspecting Equipment, Structures, or Material-Inspecting equipment, structures, or materials to identify the cause of errors or other problems or defects.
- Getting Information-Observing, receiving, and otherwise obtaining information from all relevant sources.
- Controlling Machines and Processes-Using either control mechanisms or direct physical activity to operate machines or processes (not including computers or vehicles).
- Monitor Processes, Materials, or Surroundings-Monitoring and reviewing information from materials, events, or the environment, to detect or assess problems.
- Identifying Objects, Actions, and Events-Identifying information by categorizing, estimating, recognizing differences or similarities, and detecting changes in circumstances or events.
- Wear Common Protective or Safety Equipment such as Safety Shoes, Glasses, Gloves, Hearing Protection, Hard Hats, or Life Jackets-Requires wearing common protective or safety equipment such as safety shoes, glasses, gloves, hard hats or life jackets
- Exposed to Contaminants-Mostly this job require working exposed to contaminants (such as pollutants, gases, dust or odors)
- Face-to-Face Discussions-Mostly you have to have face-to-face discussions with individuals or teams in this job?
- Sounds, Noise Levels Are Distracting or Uncomfortable-Mostly this job require working exposed to sounds and noise levels that are distracting or uncomfortable
- Freedom to Make Decisions-The job offers decision making freedom without supervision
- Spend Time Using Your Hands to Handle, Control, or Feel Objects, Tools, or Controls-Mostly this job requires using your hands to handle, control, or feel objects, tools or controls
- Contact With Others-This job require the worker to be in contact with others (face-to-face, by telephone, or otherwise) in order to perform it?
- Exposed to Hazardous Equipment-Mostly this job require exposure to hazardous equipment
- Facilities management software e.g. Computerized maintenance management system software CMMS
- Data base user interface and query software e.g. Database software
- Spreadsheet software e.g. Microsoft Excel
- Office suite software e.g. Microsoft Office
- Electronic mail software e.g. Microsoft Outlook
- Word processing software e.g. Microsoft Word
- Enterprise resource planning ERP software e.g. SAP
- Calendar and scheduling software e.g. Scheduling software
- Spreadsheet software
- Internet browser software e.g. Web browser software
- Abrasive stones e.g.Abrasive rubbing stones
- Abrasive drums e.g.Abrasive wheels
- Adjustable widemouth pliers
- Adjustable wrenches
- Metal band sawing machine e.g.Bandsaws
- Power saws e.g.Bench saws
- Manual press brake e.g.Brakes
- Power buffers e.g.Buffing machines
- Hoists e.g.Chain falls
- Compressed air gun e.g.Compressed air guns